Timber Finishes
At Lunniss Furniture I use a combination of finishes depending on the timber species, the type of figuring on the timber, the tastes of the client or the budget available.
Hard Wax Oil
HWO has become the “go-to” for the vast majority of woodworkers out there. It dries extremely quickly, provides reasonable protection, is food-safe and importantly, very easy to repair.
I use “Oil-Natura Hartwaschoil”, partly because I take every chance I can to mention that I can speak German, and partly because it has the highest wax content of all hard wax oils, by a considerable margin. Many claim to be a one-coat solution; this is the only one that actually lives up to this claim.
It leaves a soft-feeling matte finish that suits contemporary furniture, and does not darken the timber furniture or discolour with age.
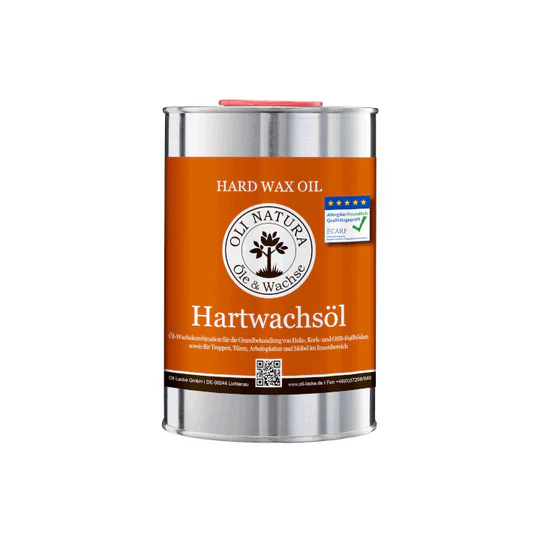
Shellac
This is the best finish for timber furniture, whether solid wood or veneer, bar none. It creates a deeply, lustrous beauty that brings out the natural colour and grain of all timbers, and enhances the light-play effect of figured timbers. It is staggeringly beautiful.
Shellac is a natural resin secreted by the female lac bug and creates a smooth, hard finish on furniture. It is dissolved in ethanol and applied in thin, even layers to create a glass-like surface.
I often use shellac as a sealer or undercoat due to its ability to bring out the natural colour and grain of wood. In application it is touch dry in a few minutes, and is absurdly easy to repair.
I only use the world’s best shellac: U-Beaut shellac, which amazingly, is a company based in Moolap.
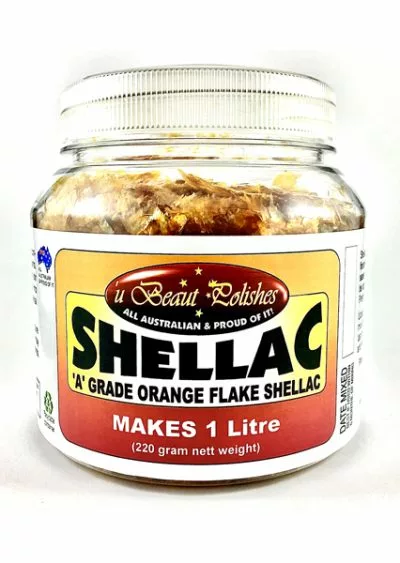
French Polish
The ultimate expression of shellac as a furniture finish, french polish is actually a technique in which shellac is applied in a circular rubbing motion using a wad of cotton or lambs wool wrapped in linen. Hundreds and thousands of layers are built-up to create a glossy, rich and wonderful finish.
It takes great skill and time to apply well (which is the main reason it has fallen out of favour in commercial furniture making). You may have heard the phrase “piano finish” – the perfect French Polish adorns Steinway pianos.
Modern tastes tend to prefer a slightly less glossy appearance. In this case I “knock back” the gloss by applying a Carnauba-based furniture wax with 20,000 grit sand paper that tames the gloss but doesn’t diminish the polish’s beautiful enhancement of highly figured timbers.
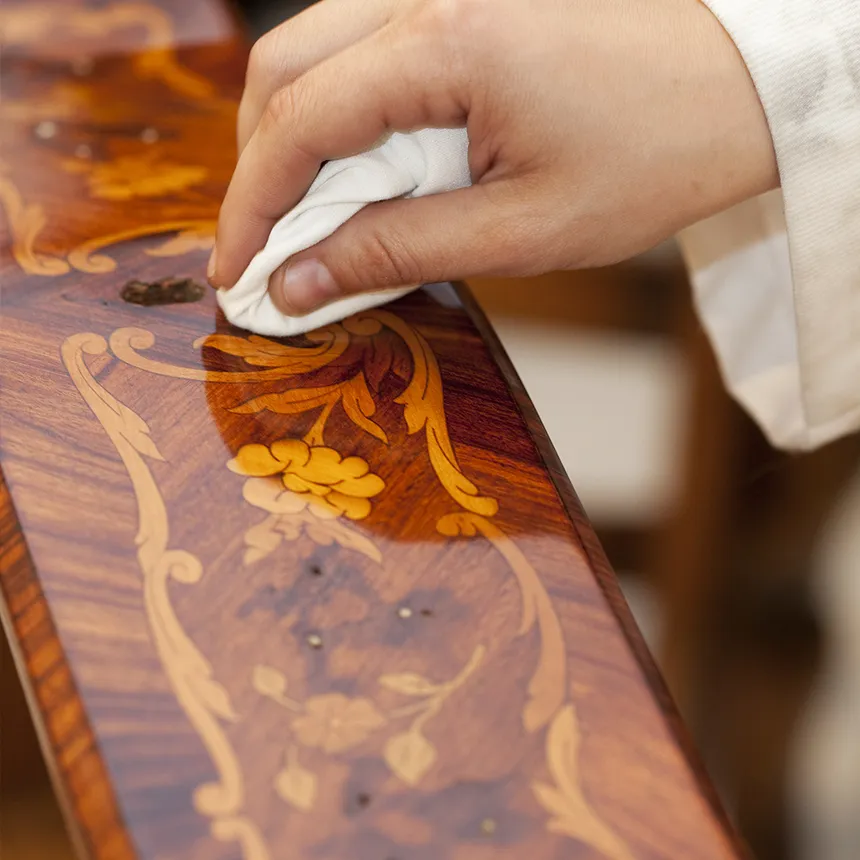
Hand-rubbed Oil
I prefer a hand-rubbed oil/varnish finish on all my solid wood furniture and components.
For darker timbers such as Blackwood I use a traditional of Linseed Oil, citrus solvent, pine turps and Tung Oil (sometimes called “Danish Oil”). The oil provides deep penetration, enhancing colors, contrast, and leaving a luxurious natural feel. It is also completely free of toxic hydrocarbons, so I get to keep my lungs. I apply this oil with a burnishing technique that drives the oil deeper in the wood fibres and reflects light from deeper into the timber.
For light coloured timbers, such as English Sycamore or QLD Silver Ash, I use a Tung Oil applied again with a burnishing technique. This is my favourite way to finish light timbers, as it doesn’t yellow over time and leaves a pleasingly low-sheen-but-still-sheeny surface that feels incredible to touch but doesn’t change the natural colours of the timber any more than water would.
In both cases the oil finish is polymerised instantly by the burnishing process, rather than taking months to cure without the burnishing.
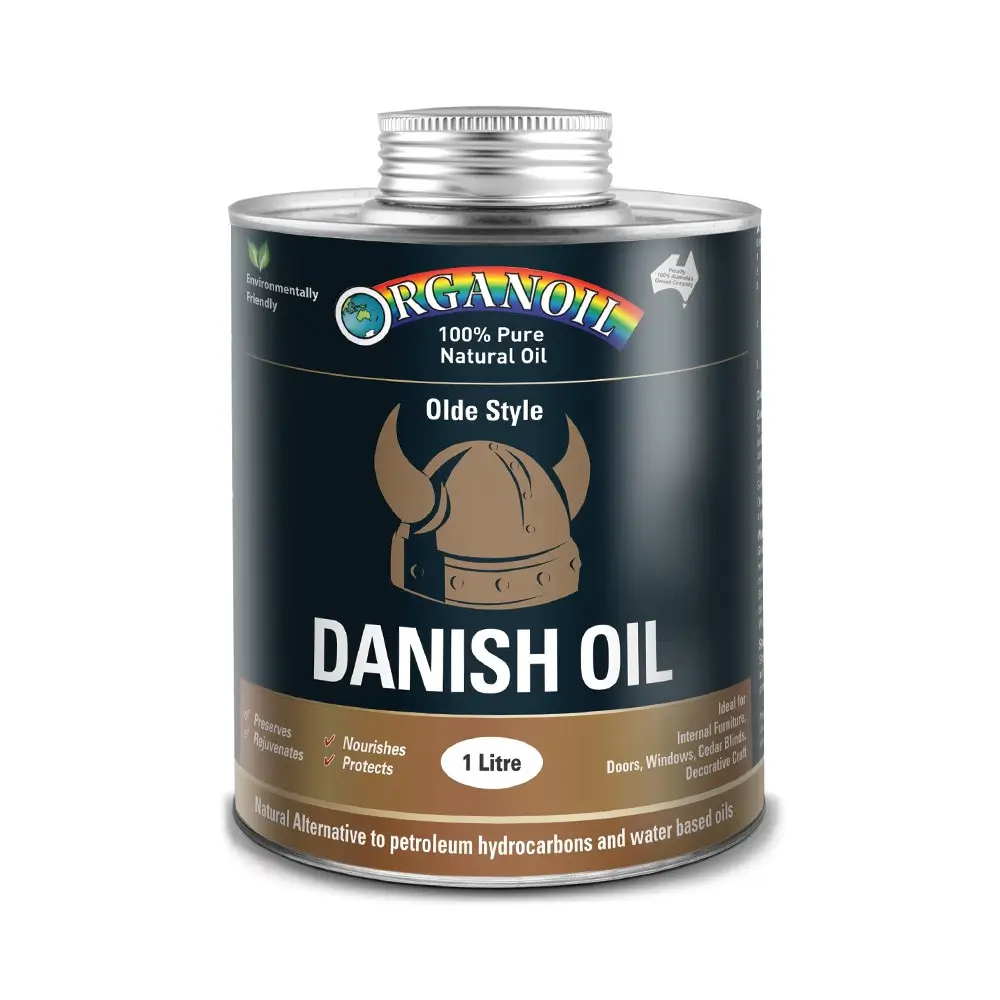
I avoid nitrocellulose lacquer, a common finish on modern furniture, due to its intentionally short lifespan, the fact that it is impossible to repair or maintain, and the fact that it has an unfortunate side-effect of shortening the lifespan of those who work with it (it is HIGHLY toxic).
When selecting a finish I take into consideration the type of timber (dark, light, figured or plain), and the ultimate use of the piece. French Polish is staggeringly beautiful, but not suitable for a dining table or kitchen workbench. The burnished oil finish is the best “feeling” finish for pieces that are touched often (chairs, table surfaces) but takes about 10 times longer to apply than a hard-wax oil, so increases the cost of the piece considerably compared to hard wax oil.
The right finish is essential for a quality piece of custom furniture, and something that too many makers neglect in favour of speed. I prioritise not just longevity, but repair-ability, guaranteeing the materials and craftsmanship of your custom furniture for your lifetime.